In many ways, the story of Cobot is the complete contrast to traditional pre-2010 industrial robots. Cobot automation is designed with the end-user in mind to make industrial automation simple, safe, and affordable.
There are numerous examples of genuine wins and opportunities in industry media, but some misconceptions are constantly propagated against collaborative robots. This article will cut through the hype to create a balance between collaborative robots, conventional robots, and interconnected issues.
Opportunities
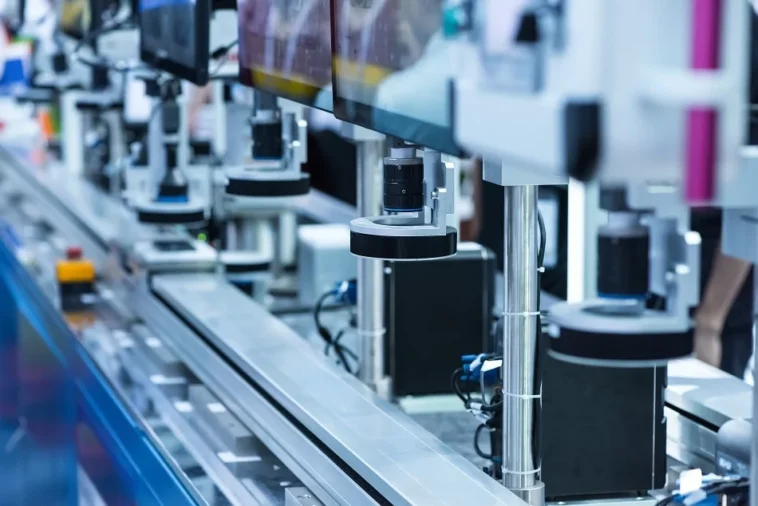
Collaborative robots are a great step forward in industrial automation. However, the most significant developments are driven by broader industry shifts: Small and medium businesses find automation more attractive. Consequently, encouraging industry players to focus on the end-user and simplifying processes.
The most significant barrier to automation for SMEs is typically a lack of confidence. In many circumstances, investing in industrial automation makes financial sense, but organizations are hesitant to take the plunge due to fear and lack of trust. As the initial step toward automation, stakeholders can now be presented with a far less intimidating cobot system. For more information, visit universal-robots.com.
Aside from the cobot technology, all manufacturers have emphasized training and breaking down the abilities into manageable chunks.
They have cheaper initial expenses and are simple to program even if you have no prior programming skills, thus they provide a quick return on investment.
Collaborative robots are now easier to integrate and do not require experienced robot engineers; they have simple features that make them even more user-friendly. No expertise is needed to operate them. Also, Cobots are great teaching assistants for beginners because they possess all the concepts required to guide novices.
The Reality Of Cobots and Robots
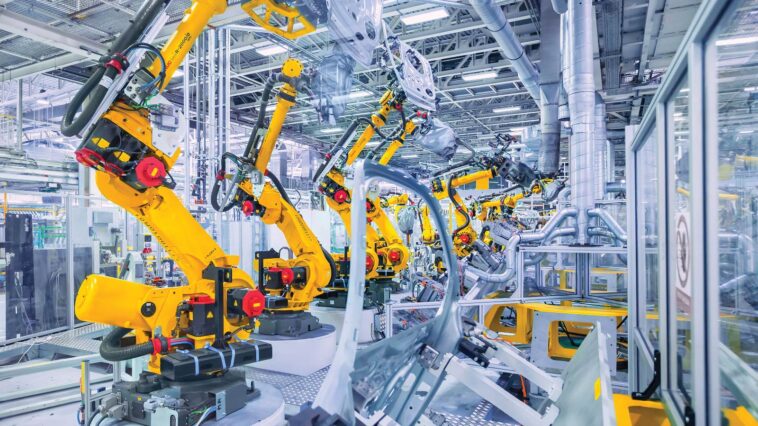
While collaborative robots have opened many unprecedented doors, the company receives resistance from “traditional” industrial automation and robotics. There is a dominant narrative that Cobots are taking the place of conventional robots. This is far from accurate.
In fact, Cobots do not substitute Industrial Robotics; instead, Collaborative robots and conventional Robots are complementary.
The large robot companies have been manufacturing robots for six decades and have mastered all of the traditional elements to high art; however, the entrance of Cobots has caught them off guard.
In the flurry of excitement surrounding Collaborative robots, it’s easy to overlook how far industrial robotics has come and how much more is still to be dreamed. What is frequently underestimated is how sophisticated modern machines have gotten and all of the various features that can be added at a bit of cost.
When to adopt a Cobot for automation
The collaborative aspect of a Cobot is the ability to work with humans on the same product, in the same space, and simultaneously. For instance, think about a technician assembling electronics and then commanding a Cobot to fasten the screws. Its flexibility provides options that can be exploited to suit any industrial operation better.
The most notable advantage provided by a collaborative robot is its flexibility and ability to adapt to manual operations. This ability makes it more reliable compared to the conventional robot. These ultramodern automation machines have three distinctive characteristics;
- They are true collaborative applications.
- Can be integrated into new product lines and operations
- Can move from one point to another within a factory environment without posing a threat to workers
Myths surrounding Cobots
Myth 1. Cobots are dangerous
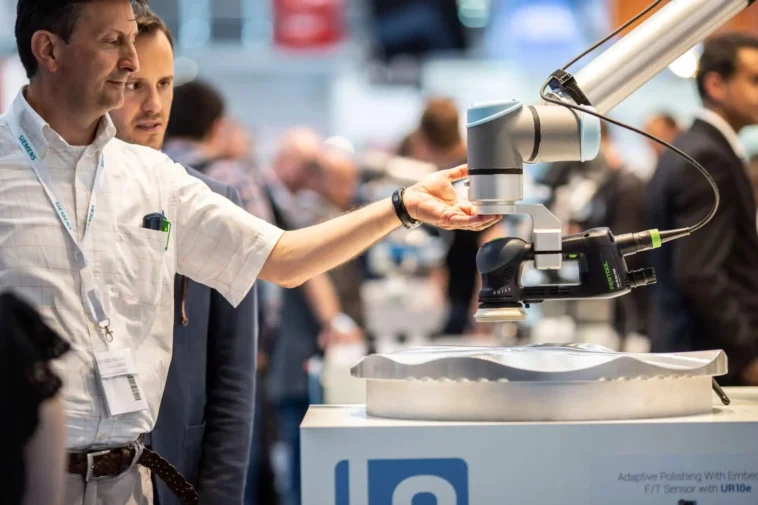
Employee safety is critical For firms looking to integrate machines and human beings under the same manufacturing roof. One of the reasons why the manufacturing industry is rapidly using collaborative robots is this.
What distinguishes them from their industrial robot counterparts is their safety. Cobots are robots that replicate human behavior. They have reduced weights and speeds and safety features such as automatic shutoff sensors. These safety technologies detect and respond to dangerous human proximity, allowing them to work alongside humans.
Myth 2. Cobots destroy jobs
Cobots in industrial settings have the potential to help a company create and retain jobs. Workers can be relieved from dangerous, exhausting, or repetitive jobs by incorporating them into their daily operations. It could also lead to new jobs that need different sets of skills, resulting in no net employment loss.
Machines cannot replace human creativity, critical thinking, and decision-making. Furthermore, increased productivity due to cobot integration may lead to more hiring. Companies can enhance productivity while also providing job possibilities for workers to handle the extra output by incorporating collaborative robots into the manufacturing process.
Myth 3. Cobots are only for large companies
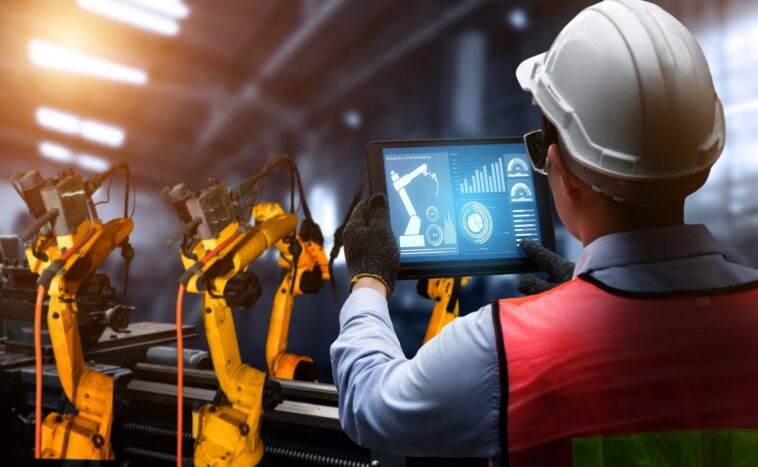
Collaborative robots are built to be simple, precise, and easy to integrate into practically any process or workspace. Conventional industrial robots have traditionally been too heavy and expensive for small to medium-sized businesses to contemplate. Pick and place, packaging and palletizing, screw driving, gluing, welding, and other simple but repetitive or demanding jobs can all be automated with them.
Myth 4. Cobots are expensive
Collaborative robots are more cost-effective than conventional industrial robots since they do not require expensive professional specialists or extensive infrastructure improvements to install. They may be repurposed to perform various manufacturing jobs and run around the clock, lowering production costs by up to 20% and providing a return on investment in less than a year.
Myth 5. Cobots are challenging to install
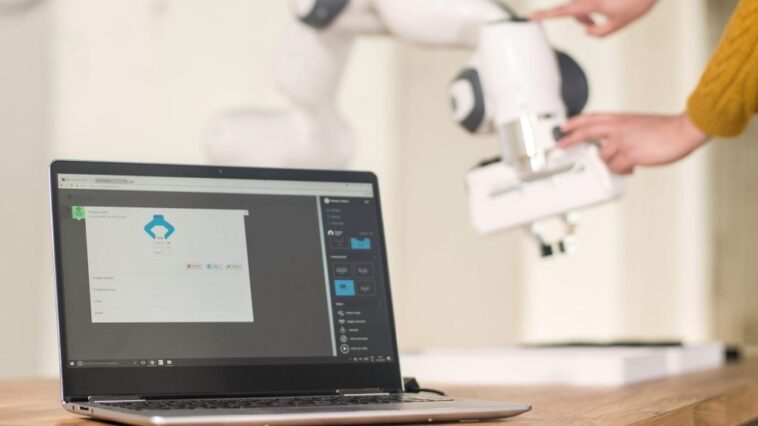
Cobots are compact, easy to install, and require low maintenance; they weigh as little as 11kg. They can be quickly installed without changing the production structure and redeployed between activities where transition times can be reduced by 50%.
Bottom line
Due to a lack of knowledge of the actual benefits and implications of cobot adoption in various industries, there has been an increase in misconceptions.
One of the primary elements that attract industries to collaborative robots is their ease of use. They don’t require costly manufacturing upgrades or installation initiatives. They also don’t need deep knowledge of proprietary programming languages. Many cobots may be programmed using simple apps or manipulating the unit physically to “teach” motion.
Beyond the misconceptions, one thing is sure: collaborative robots provide their users with a significant competitive advantage. They benefit businesses, industrial workers, and the global economy.